Mechanical Projects
An assortment of non-aerospace but often equally safety critical projects
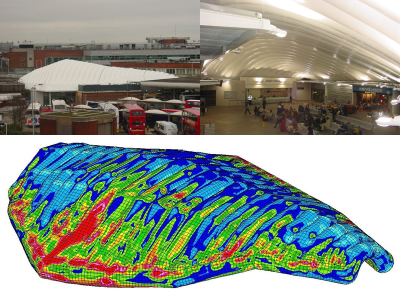
Aeromechanics performed the preliminary sizing analysis of the worlds first permanently installed inflatable roof structure for Lindstrand Technologies. The installation is sited at Terminal 2 of Heathrow airport and had to be designed to withstand all weathers. A wholly independent company performed the structural analysis of the inflatable roof to satisfy building requirements and Aeromechanics was selected to independently review their analysis.
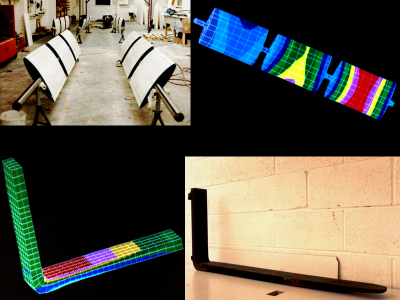
Blades for controlling the upstream pressure at RAe Pyestock’s wind tunnel test facility. The customer required the minimum blade chord thickness possible to maximise the flow through the tunnel. Aeromechanics optimised the blade’s composite lamination construction using Finite Element Analysis and the sister manufacturing company Hybrid Composites Ltd manufactured the six triple blade structures.
Bottom left and right:
A design investigation for a lightweight composite fork lift truck fork.
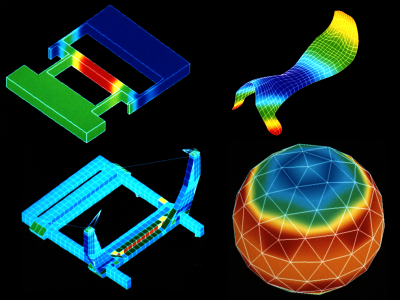
Top left: A strain gauge design for improved accuracy and stability.
Top right: Mixing old with new, a composite ‘tree’ optimising flexibility and strength for the core of a leather horse saddle.
Bottom left: A mobile engine cradle for large jet engines undergoing routine maintenance.
Bottom right: A hexagonal/pentagonal geodesic structure for a lightweight design exercise.
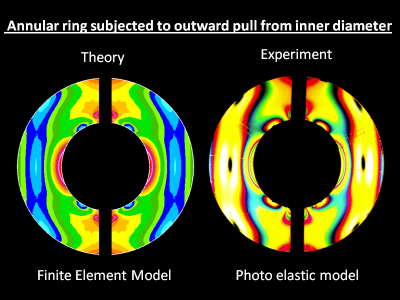
The pictures opposite show how closely modern simulation tools can match results compared with physical tests.
The Finite Element Model on the left is a numerical solution whereas the photo elastic model on the right is a physical simulation using a special resin and light source.
Interpretation of the photo elastic results require the fringe order to be accounted for to determine the actual stress level seen in the Finite Element Model. Observing the contour shapes in both pictures then shows that the correlation over the whole shape is remarkably similar.
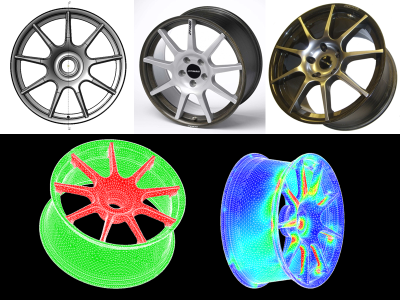
Aeromechanics performed the structural Finite Element analysis on the Dymag Racing carbon fibre composite
rim with magnesium alloy hub and spokes. Aeromechanics also established the composite design allowables for this first of a kind production component.
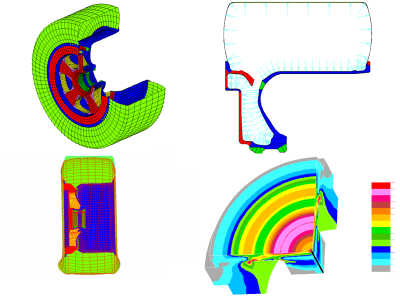
Indy 500 rear wheel stress analysis using non-linear solution techniques with hyper elastic material properties to simulate the tyre characteristics.
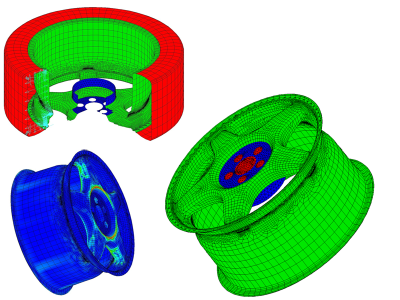
Experimental all composite wheel for Dymag Engineering. The rim and spokes were all composite and the central boss (blue and red) were of metallic construction.
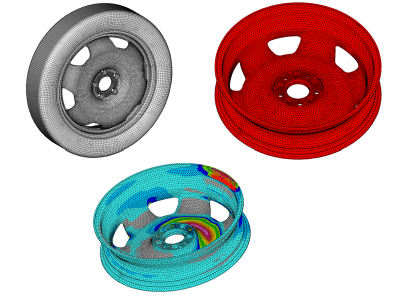
A get you home spare wheel for a world leading manufacturer of exclusive luxury cars. A plethora of additional load cases were assessed to cater for extreme driving conditions.
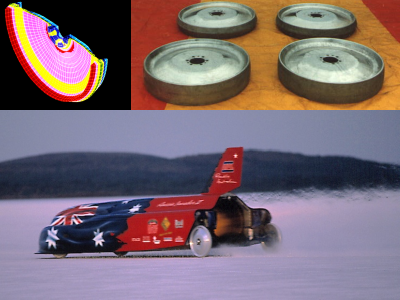
Performed structural analysis of the Aussie Invader III wheels designed by John Ackroyd for over 8,000rpm. Top speed achieved by the car was 638mph (1,028km/hr).
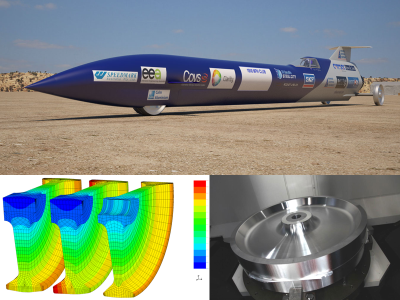
Aeromechanics are currently engaged in Rosco McGlashan’s Aussie Invader 5R assisting John Ackroyd to design the wheels for 1,000mph (1,600km/hr).
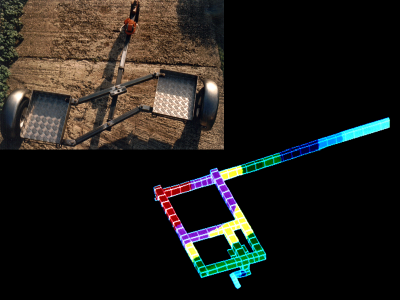
Structural analysis of a towing dolly that can be dismantled and packed in to the tow vehicle afterwards for unhindered travel.
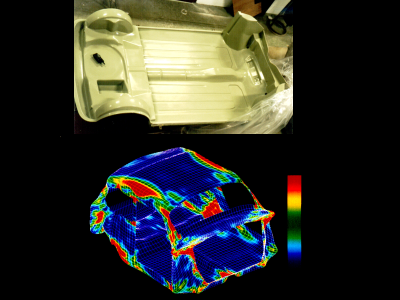
A Mini sprint for racing is a cut down version of the old style British Mini. After modifying the steel bodywork shape it was digitised and the data processed to create a Finite Element Model. The client wanted then to have the Sprint manufactured from carbon fibre composite to minimise weight whilst maximising torsional rigidity and strength. Aeromechanics performed the structural optimisation in composite materials by constantly comparing the same versions in steel and carbon to make sure there was no loss of integrity but always improved performance.
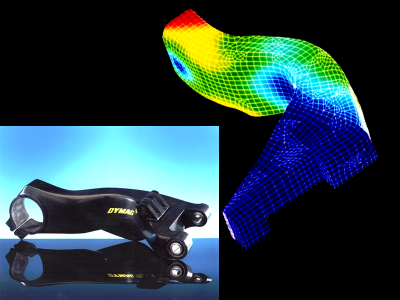
Aeromechanics Ltd were approached by Dymag Engineering to assess the structural integrity of a prototype carbon fibre single sided swing arm for a racing motorcycle that was undergoing tests.
Aeromechanics stipulated the requirements for a materials test programme and analysed the results to determine structural strength and stiffness properties for the simulation input data.
Models of both the aluminium alloy and composite swing arms were analysed and compared to ensure there was no loss of performance.
A carbon fibre design had the advantage of having less weight than the alloy counterpart and hence able to react to the track surface more rapidly.