Rotary Wing Projects
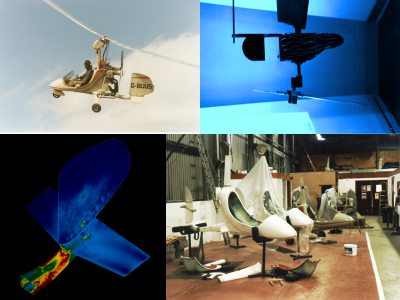
Top left:
Calculated flight loads, produced structural test plans, conducted load tests and certification test reports for the entire composite structure of the Sycamore Aviation Ltd Skyraider gyroplane.
Top right:
Oversaw University wind tunnel testing of basic gyroplane configuration for stability characteristics.
Bottom right:
Produced the documentation required for the successful granting of UK CAA manufacturing approval for all the composite components of the Skyraider gyroplane.
Bottom left:
Performed Finite Element Analysis on the composite primary structure and in particular torsional stiffness assessment of the tailplane.
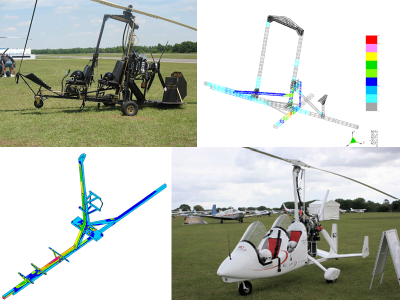
Top left & top right:
Exploratory Structural analysis of a Parsons Gyroplane fitted with a Mazda Rotary engine.
Bottom left:
Performed Finite Element Analysis of the primary airframe structure for both in-flight and emergency landing cases.
Bottom right:
Initial structural certification analysis on the complete Magni M16 two seat Gyroplane for UK CAA BCAR Section T approval.
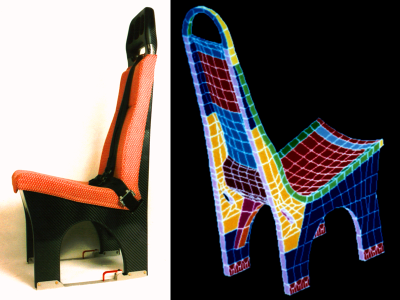
Aeromechanics Limited were approached by an aircraft interior furnishings company specialising in executive passenger seating. They were looking to advance their products by utilising lightweight composites. Their client was looking to reduce the overall seat structural weight in their helicopters to increase the total number of passengers flown per ferry flight for offshore oil exploration operations.
Aeromechanics provided the expertise in advanced composite material design, analysis and structural optimisation. In addition to the Finite Element Analysis undertaken, Aeromechanics derived the material characteristics through an extensive coupon test programme.